The 2025 Hiring Outlook for Industrial Automation
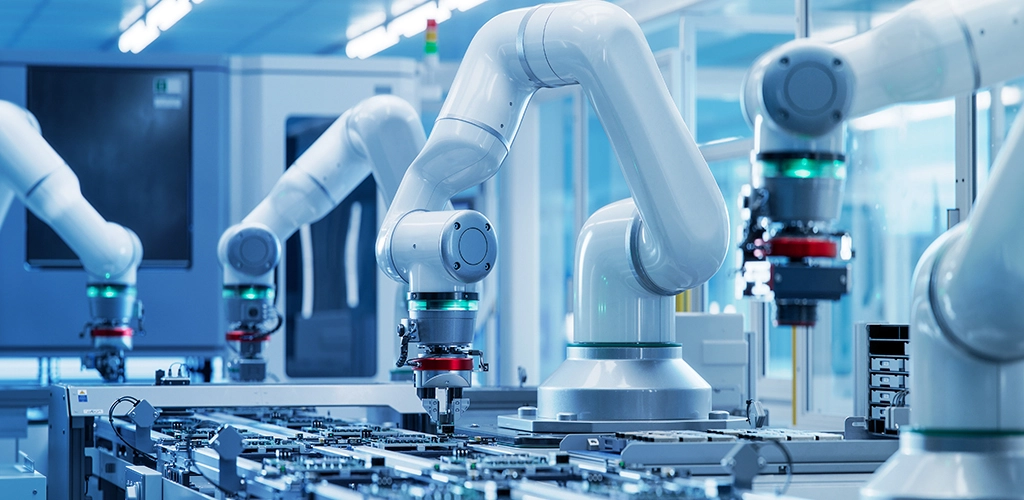
The world of Industrial Automation is expanding at warp speed today, bringing with it a robust demand for more and more specialized talent. This article provides a snapshot of the current hiring landscape, giving employers like you the insight that you’ll need to harness the outlook to your advantage in 2025.
Revolutionary growth
As expected, the ongoing development and adoption of new technologies will continue to transform and modernize the Industrial Automation market in 2025. More companies today are using sophisticated technologies like soft programmable logic controllers, artificial intelligence, and machine learning to solve relatively common workflow challenges, so the landscape is changing every day. It’s not hard to see why. Advantages include increased efficiency, control, precision, and better cost-effectiveness.
The global Industrial Automation market reached $193B in 2023. It’s now estimated the segment will exceed US $295 billion by 2028, as companies optimize their efficiency and return on investment in Industrial Automation systems through these advanced technologies—in turn, driving demand for people with the skills to leverage them. The market should grow at a CAGR of 8.6% to reach $402B by 2032.
Because soft PLCs are easy to modify, and easy to integrate with the computer systems and handheld devices used in industrial settings—they can also serve as one viable solution to the existing skilled labor shortage challenges. They help to adapt newer technologies to meet changing operational needs, so they’re gaining popularity across energy, smart manufacturing, petrochemical, and other process-driven industries. Meanwhile, AI and machine learning provide insights for optimizing processes and automation by analyzing complex data sets and using the results to improve future system designs.
Growth factors
This convergence of individual technologies, used in combination to create an immersive three-dimensional virtual industrial environment, have been coined the industrial metaverse. According to a recent study, 92% of surveyed manufacturers are already experimenting with or implementing at least one metaverse-related use case, and on average, they’re currently running more than six use cases.
Moreover, many organizations today are choosing to use automation services because they lower their reliance on manual labor, ensure a faster pace for mass production, and enhance the speed of production processes. That reduces the consumption of electricity and other resources, also making the manufacturing process cheaper—one more tool for navigating a challenging labor market. Another major growth-inducing factor for the market is the consistent demand for efficient automated systems. And due to a significant increase in industrialization and urbanization, the need to automate repetitive tasks and streamline the business process has also been increasing across different industries.
Reaping the benefits
A recent Deloitte study showed a striking 86% of surveyed manufacturing executives believe that smart factory solutions will be the primary drivers of competitiveness in the next five years. Manufacturing executives anticipate an increase of 12%+ in several key performance indicators, including sales, quality, throughput, and labor productivity because of industrial metaverse initiatives—which might also help to address the ongoing labor shortages.
Other advantages of Industrial Automation cited by leaders include:
- Improved productivity – by automating tasks that workers traditionally do, a company can free up time and resources to focus on more critical tasks, for increased efficiency.
- Optimized costs – robotics, AI systems, and other technologies can minimize production, labor costs, plus the cost of errors and downtime, with less maintenance.
- Enhanced quality – by automating some steps in the manufacturing process which are difficult for humans to do accurately, like welding, measuring, and packaging.
- Better workplace safety – IoT devices can help to track machinery damage, toxic material, vehicle mishaps, or other potential hazards and take steps to mitigate them.
Of course, while automation can propel manufacturing forward, you need the right talent in place to enable your Automation projects. And depending on how your business fits in the automation process—whether as a systems integrator or machine builder or component supplier—that means engaging a wide variety of specialized engineers and technicians.
Hiring outlook for Industrial Automation
We examined the hiring outlook for Industrial Automation by analyzing recent placements across the U.S. for those same various roles. The types of positions ranged from Automation Engineers, Controls Systems Engineers, Project Managers and PLC Programmers to Mechanical Design Engineers, Electrical Design Engineers, CAD Technicians, and Field Service Technicians.
The estimated number of people employed in those roles in the workforce today is about 290,000. The estimated salary ranges from $72K to $114K. We calculated demand by processing, deduplicating, and counting job postings from tens of thousands of websites across the internet—roughly 44,000 openings.
Hiring difficulty for these roles is currently expected to be moderately difficult. That score is driven by a relatively low supply of available talent, with just 9 candidates per each new job opening, which favors the candidate. The typical job posting is open for 74 days on average before, while 50% of positions are filled with 30 days. Meanwhile, although competition for that talent has decreased in the past year, it’s expected to increase and competition remains highly dispersed, divided across many equal employers. This means there isn't a single big player or employer brand dominating current openings.
We also examined the top roles required by employers for Industrial Automation positions, as well as the top locations for finding qualified candidates based on talent supply:
Fastest Growing Roles in Demand
Fastest Growing Roles in Demand
Automation solutions will continue this year to offer limitless possibilities across industries, with solutions that integrate various technologies. Be sure to monitor any emerging technologies, regulatory frameworks, and industry standards to keep adapting to new market dynamics. Think about training and upskilling your workers to ensure optimal utilization of Industrial Automation systems. You can further improve employee attraction and retention by leveraging digital tools, engaging retirees, and fostering partnerships within the local community.
Also consider finding a proven partner for talent in Industrial Automation like Kelly Engineering. We’re the experts at hiring experts. In a tight labor market with only 9 candidates available per open role, we can ensure you fill your position. About 35% of our talent pool is not actively on the market—not found on job boards or resume sites, but only through Kelly Engineering. And we continue to build out this pool of talent with unique recruiting strategies like our (Ex)2 Expert Exchange series or our LinkedIn Live events. We carefully screen and select candidates so that you’re getting the most qualified workers for your business needs.
Then we work with you to develop a staffing solution that meets your budget and timeline. That means flexible options to fit your need whether it’s a contract role, direct hire, or full project service. Our statementworX suite offers a highly customized set of managed solutions that can help to solve your most critical challenges for Industrial Automation through the near future. And we don’t get paid till you fill the role or complete the project, depending on the solution you choose.
As a niche recruitment specialist, Kelly Engineering is ready to partner with you. We provide a full portfolio of customized talent solutions to complement your business needs that includes contract, contract to hire, direct hire, and managed solutions through statementworX, where we manage an entire team, project, or function according to your requirements.
Icon cards headline here.
Card Two Title
Lorem ipsum dolor sit amet, consectetur adipiscing elit. Integer nec odio. Praesent libero. Sed cursus ante dapibus diam. Sed nisi. Nulla quis sem at nibh elementum imperdiet uis sagittis.
Card Three Title
Lorem ipsum dolor sit amet, consectetur adipiscing elit. Integer nec odio. Praesent libero. Sed cursus ante dapibus diam. Sed nisi. Nulla quis sem at nibh elementum imperdiet uis sagittis.
Card Three Title
Lorem ipsum dolor sit amet, consectetur adipiscing elit. Integer nec odio. Praesent libero. Sed cursus ante dapibus diam. Sed nisi. Nulla quis sem at nibh elementum imperdiet uis sagittis.
“After witnessing two school systems that have successfully deployed a KES solution for their substitute staffing needs— along with the subsequent savings in hard and soft cost, time, and critical resources that our schools have realized— the question I typically ask any district on the fence is … ‘Who couldn’t afford to implement a KES program?’”
— Dr. Michael Henry, HR Director of Instructional Personnel, School District of Clay County
We've got work figured out.
In calm or chaos, you can count on us for guidance. Because we’ve been around, and we’ll be here for you. We know a thing or two about the future of work—and we can’t wait to help you discover what’s next.
Contact us at 800.Kelly.01 and one of our agents will administer your request. Or, if you’d prefer, fill out the form to submit an email.